What Is Six Sigma? The reality of a business or organization is that for its efforts and accomplishments to flourish and advance to another level, improvement of both the quality and processes of its product and services is vital.
“Success is not final; failure is not fatal: it is the courage to continue that counts”.
– Winston Churchill
This simplifies how a business can only thrive when it takes up new momentum to hone its potential. Many people may think that as long as the elements like employees’ performance, financial health, budgetary allocation, workforce, technology and infrastructure are secured, the success of the business can be sustained.
However, that is not the case for the growth of a business in the long run if the processes within the business are poor, lack in quality and produce a lot of waste and defects. This is why people of different careers and background took their time to explore ways to help improve the vitality of a business and diminish as much waste as possible. Hence, a process, quality, and waste reduction management methodology; “Six Sigma” was born.
WHAT IS SIX SIGMA?
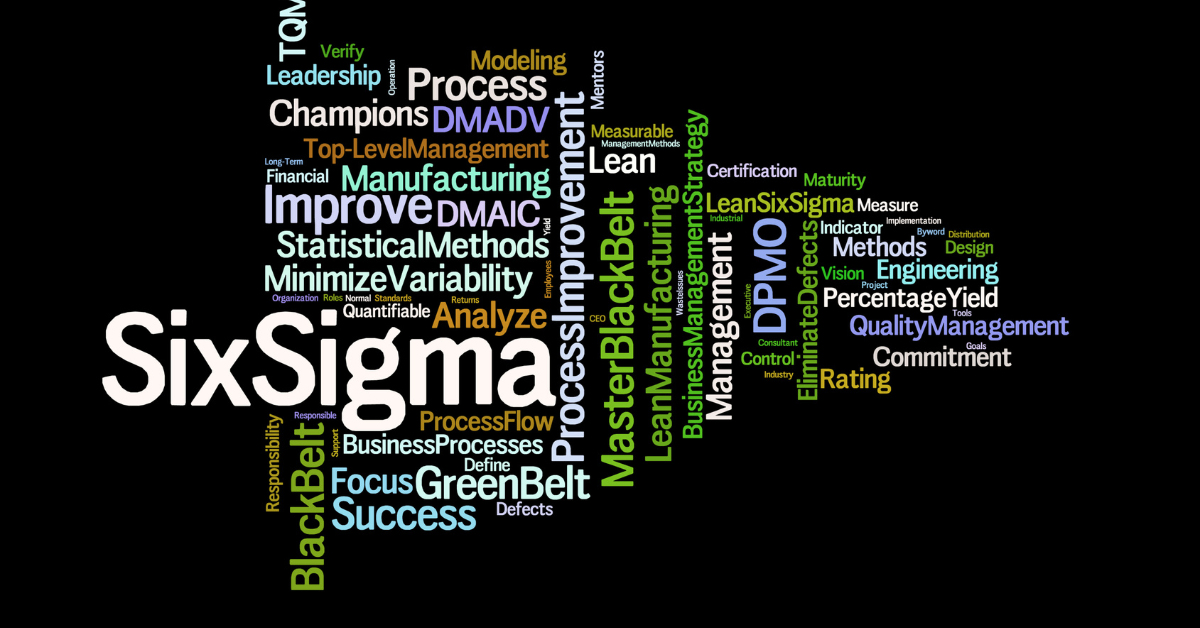
“Six Sigma” is a methodical, structured approach that works in tackling organizational issues through the elimination of variations and reduction of risks (Lean vs six sigma, 2020). It works in removing inefficiencies, and determining a defect as anything that does not meet the expectations and satisfaction of the customers (Johnson, 2020). In addition, Six Sigma focuses on creating new processes or improvement processes when the end solution is unclear and hard to handle. The statistical methods in Six Sigma are used to measure and analyze current trends, and make data driven decisions to achieve the optimal process.
The ultimate goal of Six Sigma is to eliminate waste and increase the efficiency of a system as much as possible, and achieve consistent result (Johnson, 2020). In Six Sigma standard, the quality of a production process within an organization should only produce 3.4 defects per million opportunities which means 99.9997% success rate that can be considered as a world-class performance (What are the differences between six sigma, lean and lean six sigma, 2020; Aruleswaran, 2009). For example, in the air travel industry, if a country has over 1 million takeoffs and landings a year, the industry will have a probable 6,941 number of takeoff or landing mistakes. However, by using Six Sigma, that number will drop drastically to only 7 probable mistakes.
HISTORY OF SIX SIGMA
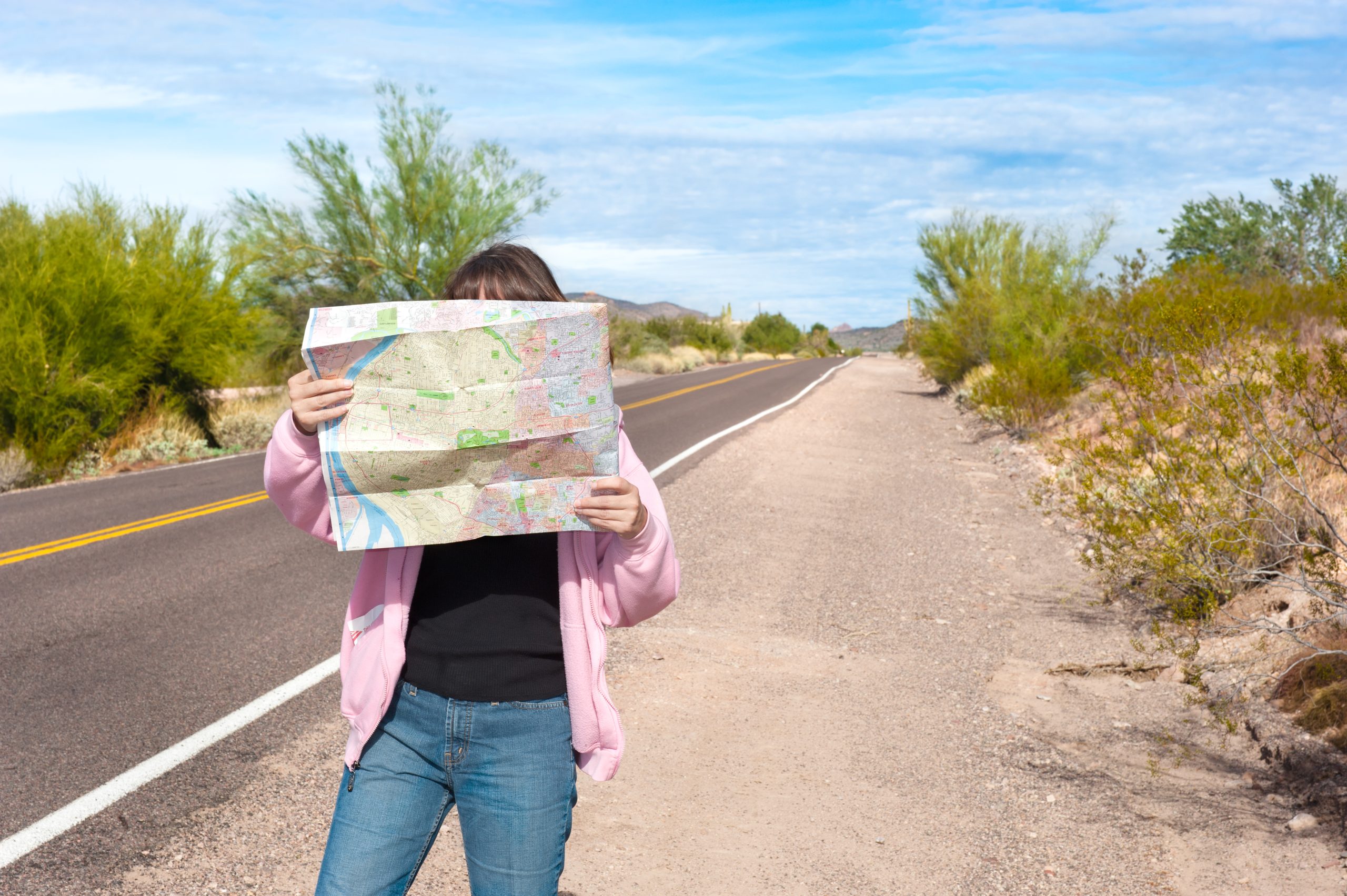
In the 1980s, an engineer at Motorola Corporation under the name of Bill Smith developed the concept of ‘Six Sigma’ in other to promote quality and eliminate defects in manufacturing (Kumar, 2020; History of six sigma, 2018; Pepper & Spedding, 2010). This development has been a great help to Motorola to be the first company to receive the Malcolm Baldrige National Quality Awards in 1988 (History of six sigma, 2018). Today, due to his concept invention, Bill Smith is now known as the ‘Father of Six Sigma’.
In addition, the credit also goes to Jack Welch – previous CEO of General Electric (GE) – who popularised the Six Sigma concept. GE adopted Six Sigma with the guide of Allied Signal (the second company who adopted Six Sigma) after Lawrence Bossidy of Allied Signal was mentored by Jack Welch himself during Bossidy’s employment at GE (Pepper & Spedding, 2010; History of six sigma, 2018; Olofsson, n.d.). Ironically, a “student becomes the teacher” event can be seen to have happened here. That said, Six Sigma was widely spread to many organizations and has become such a popular and effective quality management methodology until this very day.
THE FUSION OF SIX SIGMA AND LEAN
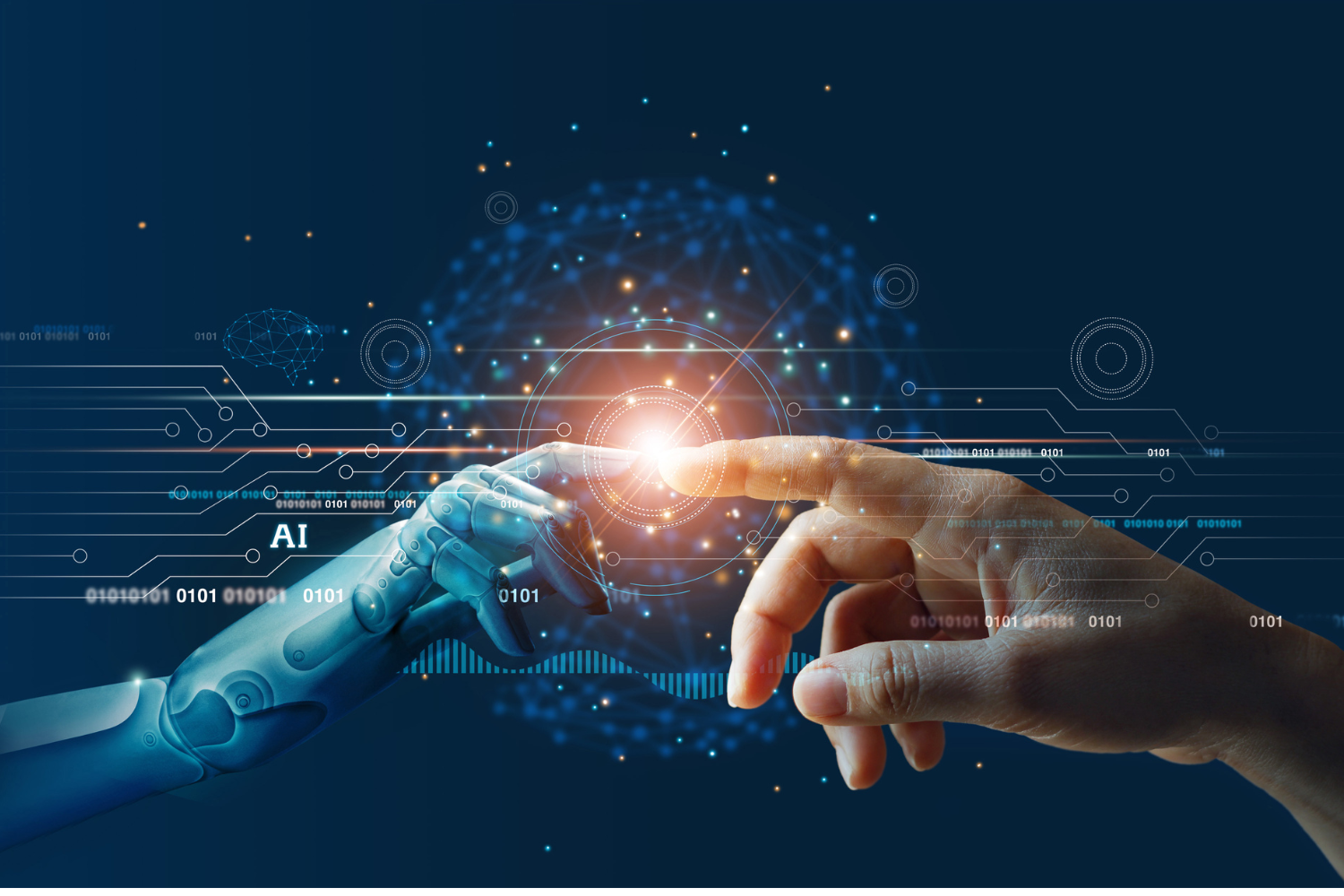
While Six Sigma was introduced in the 1980s, Lean (a.k.a. Lean Thinking) was introduced earlier in the 1930s by founder of Ford Motor Company, Henry Ford, before it was modified by the Toyota Motor Corporation. Lean focuses on the big picture, analyzes workflow cycle, maximize value to customers using as few resources as possible, and seeks to eliminate waste (e.g, TIMWOOD) along the entire value stream, not just isolated points of production (Johnson: What are the differences between six sigma, lean and lean six sigma, 2020).
Lean and Six Sigma is similar in terms of their ultimate goals; eliminate waste and increase the efficiency of a system as much as possible (Lean vs. six sigma, 2020). But how did these two powerful state-of-the-art methodologies fuse and applied together?
In 1986, the George Group was the first company who integrated and popularized the application of Lean and Six Sigma. Now, the use of Lean Six Sigma (LSS) has been widely known throughout the world (Salah & Rahim, 2019) as a new methodology born from the combination of two advanced business process improvement that complements and enhance one another. To illustrate, while Lean aims to create value through eliminating waste and non-value-added activities, Six Sigma measures the quality of product/service and meets the customer’s needs and satisfaction (Aruleswaran, 2009).
WHAT ARE THE METHODOLOGIES OF SIX SIGMA?
In Six Sigma, there are mainly two methodologies; DMAIC (designed to accommodate the improvement of existing processes) and DMADV (conducted for the improvement and designing of new processes). Now, to give you more insight, let us go further into the detail of these methodologies.
DMAIC
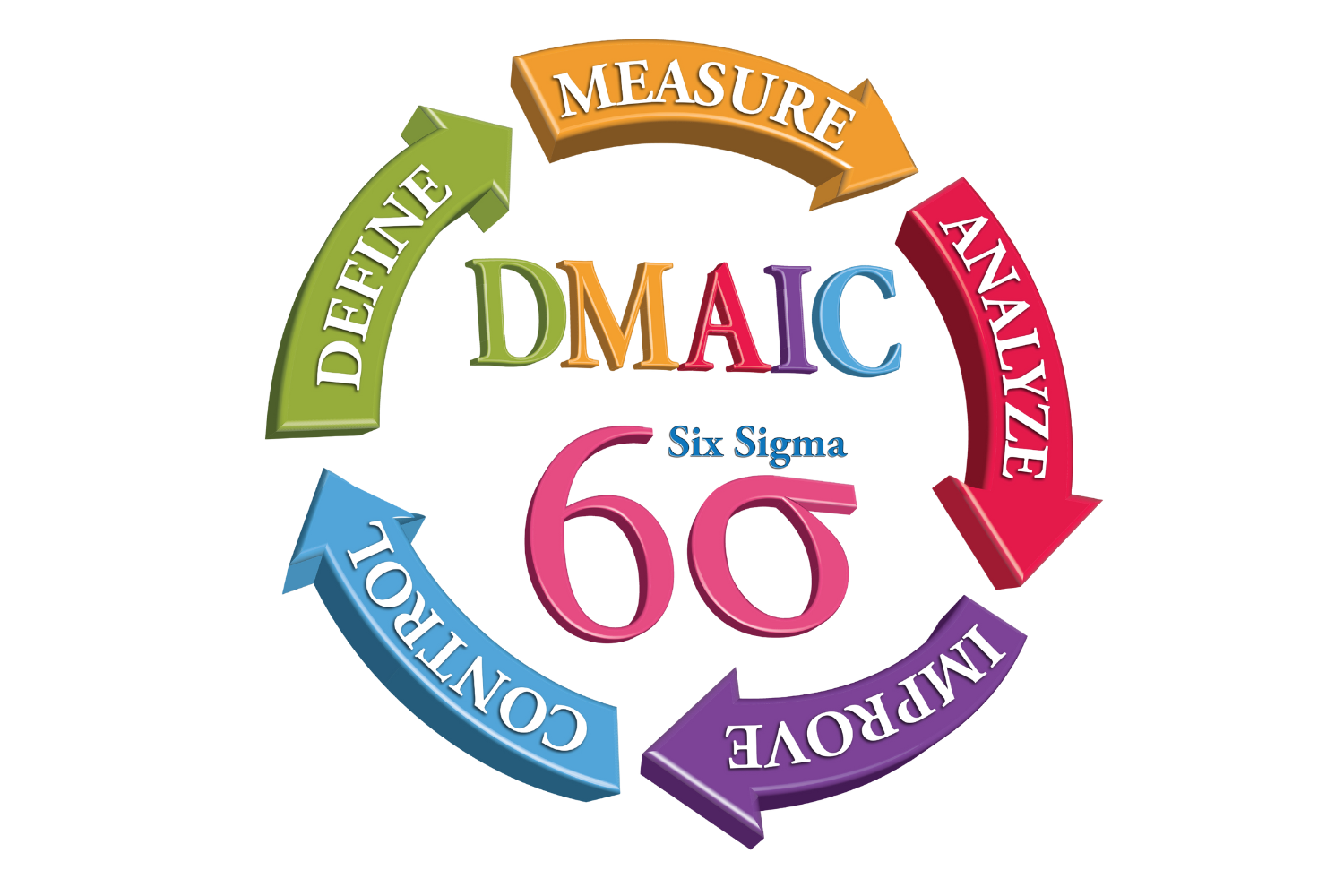
What is DMAIC?
DMAIC is DMAIC is a data-driven methodology that focuses on quality and process improvement management for better customer satisfaction. This method helps refine the projects and deliver quantifiable and sustainable results (Kumar, 2020; DMAIC – The 5 Phases of Lean Six Sigma. 2020).
D – DEFINE | Define or summarize the problem and the objectives, and determining the customers (internal or external) and their demands and requirements. |
M – MEASURE | Collect the data that is relevant with the scope of the project. Focus on the ways the parameters need to be quantified and measured via different techniques and methods. |
A – ANALYSE | Analyse the process, the factors and influence of a business’ inefficiencies, and ways to rectify and improve them. |
I – IMPROVE | Improve processes by identifying and implement possible approaches to resolve and improve organizational issues. |
C – CONTROL | Ensure improvements are maintained and monitored |
DMADV
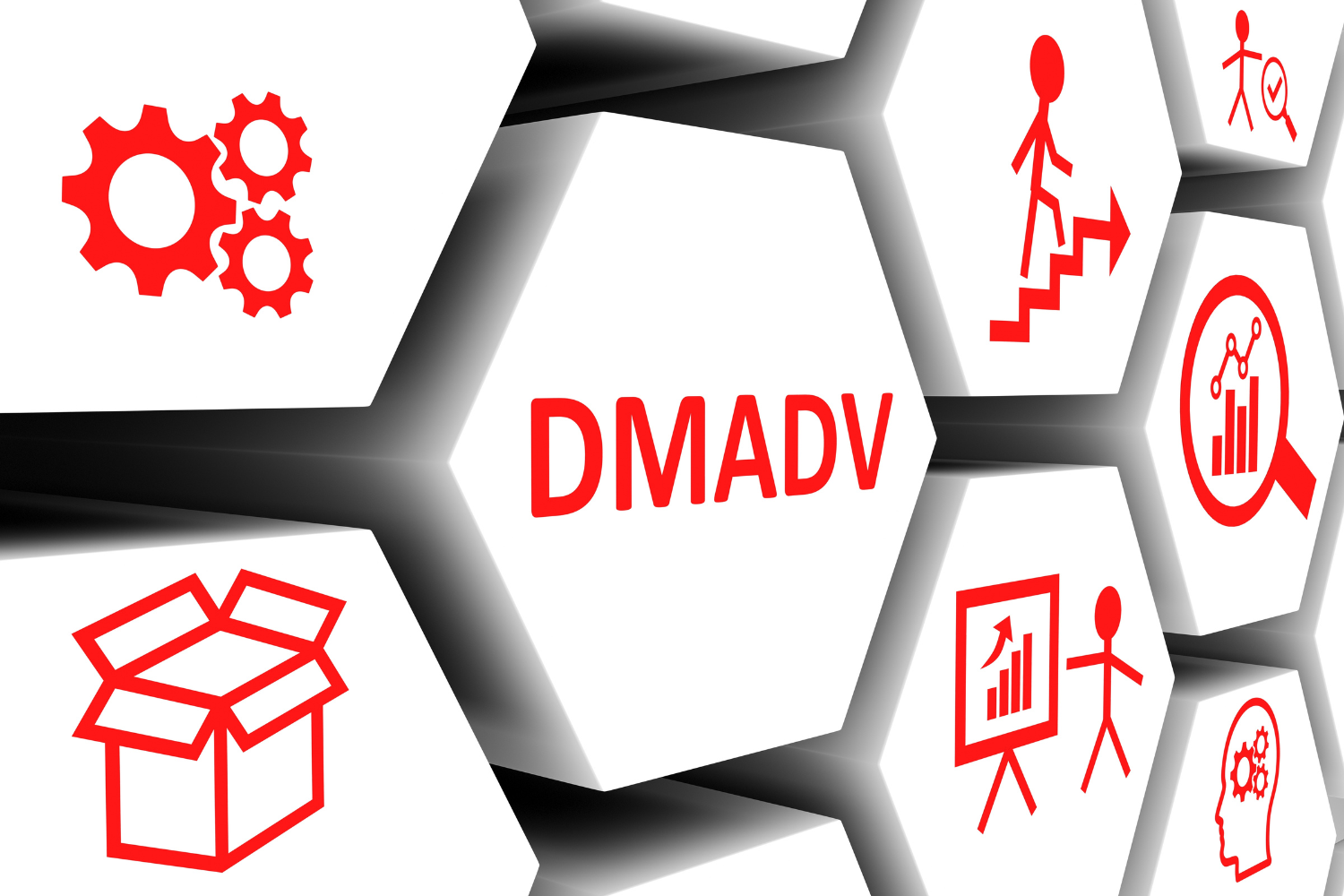
What is DMADV?
DMADV is a methodology that focuses on meeting customer’s demand and satisfaction by developing new products, services or processes when the already existing ones are ineffective and are not up to customers’ standards (Kumar, 2020; Six sigma fundamentals: DMAIC vs DMADV, 2014; What is DMADV?, 2012). Each letter of DMADV acronym stands for;
D – DEFINE | Define an organization’s project objectives, processes/services and potential outputs in order to set measurable goals according to the organization’s perspectives and estimate possible risks. |
M – MEASURE | Collect data to measure Critical to Quality (CTQ) elements by determining the conditions and market segments, critical design parameters, evaluation score sheets (to evaluate design factors, crucial to the quality), re-estimate risks and process, as well as production capability. |
A – ANALYSE | Analyse product design alternatives, determining the optimal conditions for better value within constraints, creating and evaluating theoretical designs, and choosing the best components for the best alternative design. |
D – DESIGN | Design top-level and detailed design for the chosen alternatives with prioritized design components. |
V – VALIDATE | Validate approval of alternative design to stakeholders through many quality testings; whether the new design is effective enough in the market. |
WHAT ARE THE TOOLS AND APPROACHES USED IN DMAIC?
We, in MBizM/Lean Sigma Expert Australia, prefer using DMAIC methodology more compared to DMADV as it is much more commonly used in various industries. So, here is a more detailed explanation of DMAIC where it involves five phases and within each phase contains essential tools and approaches used in a Six Sigma project.
DEFINE PHASE TOOLS/APPROACHES
This phase focuses on identifying the project’s problem statement and goals in order to emphasize the improvements needed by defining the measureable criteria or metrics. Below is some of the tools/approaches that are normally used to help the objective of Define Phase;
Project Charter | Project Charter is a documentation of important details of an organization’s project involving information on the project objectives, goals, scope of work, and representatives. It acts as contract/agreement between those involved, and used for planning measures throughout the project development and project data. |
Drill Down Tree | Drill Down Tree is a tool that focuses on breaking down ideas in progressively greater detail. The aim of this tool is to partition a problem into its smaller components. It is a convenient define phase tool as it makes the idea much easier to understand and quantify. |
Pareto Chart | Pareto Chart is a simple graphical technique for displaying data in a ranked format by category. It bases its principles on the theory that 80% of the data is usually represented by 20% of the categories (known as the 80:20 Rule). It is helpful as it allows us to make decisions on which issue is causing us the most problem and make a big impact in the efforts we put in. |
SIPOC | SIPOC (stands for Supplier, Input, Process, Output, and Customer) is a diagram that gives an overview of the project that involves all relevant elements of a process improvement project before the actual work begins. It is a high level picture of the process that depicts how the given process is servicing the customer. This tool can be considered as an advanced ‘process map’. |
VOC (Voice-of-Customer) Analysis | Voice of Customer is a tool that identifies the customers (e.g, internal, external and multiple customers), and records customers’ requirements, expectations, feedback, needs, and demands by following the CTQ (Critical to Quality). This tool is very important in a business as it helps identify the key requirements to meet customers satisfaction. |
Project Timing Plan | Project Timing Plan functions as a time management plan where a rime-line is analysed and developed for the completion of a project. It involves developing a benchmark that is deemed appropriate for a particular project, so that it will not be too short or too long. |
Project Cost/Benefit Calculation & Financial Impact (FEA) | This method is needed to calculate how much savings can be obtained from the project, whether it is hard savings (tangible savings) based on the P&L or soft savings (intangible savings) based on the risks of not carrying out the project. Example of a tool used for advanced financial calculations is;
Internal Rate of Return (IRR) Formula IRR is a metric used in capital budgeting to estimate the profitability of potential investments. |
MEASURE PHASE TOOLS/APPROACHES
This phase focuses on measuring the project current performance. In this phase, problems or improvements are mapped out in detail in which they are quantified and a baseline data is established. Below is some of the tools/approaches that are commonly used to help the objective of Measure Phase;
Revised Project Charter | Revising the Project Charter is done in order to adjust it for any improvements or changes that happen within the system or process of the project.
|
Process Map | A Process Map – aka flowchart – is a planning tool that helps in comprehending a work process/flow. This map specifies the people involved in the project and materials of the process. This tool is very useful for a project in determining the area where defects and wastes transpire, and how to improve it
|
Basic Value Stream Mapping (VA, NVA, VE Analysis) | Value Stream Mapping is an approach that records the progress and details of materials and information to plan a new project. It helps in identifying the VA (Value-Added), NVA (Non-Value-Added), and VE (Value-Enabling) activities within the process.
|
Cause and Effect Diagram – C&E Matrix | The “Cause and Effect Diagram” – aka Fishbone diagram – is a data-collection tool that functions in detecting the source of an event or effect via ‘Brainstorming’. This tool lists down data of the factors to be tested, evaluated and observed.
Cause and Effect Matrix (C&E Matrix) When you want to investigate/prioritize a certain identified causes of events, the C&E Matrix is used to help subjectively quantify the relationships of several ‘Causes’ to several ‘Effects’ and identify the ones that makes the biggest impact to the project. |
Data Collection Plan | A data collection plan is an approach used to collect baseline data or data that can point to the root cause of the problem. This approach includes questions of where, how, when and who in collecting data. Examples of tools used are;
Measurement System Analysis (MSA) MSA is a mathematical and experimental method used to determine how many variations within the measurement process contributes to overall process variability. Gage Repeatability and Reproducibility (R&R) Gage R&R is a statistical tool that helps in measuring the amount of variation in the measurement system developing from the measurement device and the people taking the measurements.
|
Z-Value Calculations/Process Capability | This approach is used to benchmark a project in order to see if its process capability is at six sigma level and has meet the project specifications (contains low number of defects) based on the calculated Z score. |
Failure Modes and Effect Analysis (FMEA) | FMEA is a tool that acts as to uncover, assess, and prioritize areas within a work process that show potential faults. This tool includes pushing those responsible of the project to verify and classify possible risk, as well as create alternatives to handle the potential failure modes and effects. |
ANALYSE PHASE TOOLS/APPROACHES
This phase’s main purpose is to detect the root causes of the problems. In this phase, data analysis is conducted in order to filter the reasons of the problems. By pointing out the primary causes of the problems, correct solutions can be implemented. Below is some of the tools/approaches that are commonly used to help achieve the objective of Analyse Phase;
Revised Project Charter/Fishbone Diagram and FMEA | Revising the Project Charter is done once more for any further changes within the system or process of the project. The Fishbone diagram and FMEA can be revised if more causes to the problems were identified. |
Graphical Analysis – Charts | This is a method of analysis that performs graphing by taking the input from the data tables and can detect the vital factors of a problem. Examples;
Dot Plots Used to assess and compare distributions by plotting the values along a number line. It is a useful tool for visually comparing distributions, display the distribution of a column of data, and gain insight about the centre and spread of the data. Box Plots Used as a basic graphing tool that displays centring, spread, and distribution of a continuous data set. |
Statistical Analysis – Hypothesis Testing (P-Value) | This tool involves the process of using statistical analysis to determine if the observed differences between two or more samples are due to random chance (null hypothesis) or to true differences in the samples (alternate hypothesis). Examples of hypothesis testing tools are;
– Normality Test – Chi-Square Test – T-Test – Analysis of Variance (ANOVA) – Homogeneity of Variance (HOV) – Mood’s Median – Welch’s T-Test – Kruskal-Wallis H Test (aka One-Way ANOVA on ranks) – Box Cox Power Transformation
|
Statistical Analysis – Correlation & Regression Analysis | Correlation analysis involves quantifying the association between two continuous variables, while regression analysis involves assessing the relationship between an outcome variable and one or more risk factors or confounding variables. Correlation and Regression analysis functions in dealing with the relationships among variables. Examples of data-analysis methods are;
– Simple Linear Regression – Multiple Regression – Logistic Regression – Nonlinear Regression – Regression for Method Comparison – Regression with Survival or Reliability Data – Regression with Count Data – Regression with Time Series Data – Regression with Nondetects Data – Two-Stage Least Squares – Subset Selection |
IMPROVE PHASE TOOLS/APPROACHES
This phase is where after the root cause of the problem is identified, solutions are generated and tested through pilot testing. The baseline data obtained from the Measure Phase is compared to the data collected from the pilot, in order to identify any improvements that can be made. Below is the tools/approaches used to help the objective of Improve Phase;
Finalized Project Charter | At this stage, the Project Charter should already be finalized as the solutions to the problems have already been generated to be implemented. |
Solution Selection Matrix | A Solutions Selection Matrix is a matrix that helps identify the best solution among several solutions identified, by weighting the impact of each solution on the CTQs (Critical To Quality) and cost-benefit; hence, measuring the effectiveness of solving the problem. |
Updated Process Map | The initial process map from Measure Phase should be updated for any change that happens within the process following the identification of the solutions. However, if there is no change in the process, then the project team need to find out where the step within the process will the solutions be implemented in. |
Cost Benefit Analysis (CBA) | Cost Benefit Analysis is the weighing scale approach to decision-making. All the elements (cash-flow and other tangible benefits) are put on one side of the balance and all the negative elements (the costs and disadvantages) are put on the other. Whichever weighs the heavier wins. |
Risk Assessments of Chosen Solutions | A risk assessment involves the process of brainstorming to identify[ the potential risks of the chosen solutions when applied and then communicating them to the Champion and stakeholders |
Pilot Plan/Solution Implementation Plan | A pilot plan is the experimental/preliminary trial of the chosen solutions by using only a small and limited scale. This step is important to determine the best elements and areas that the solutions can be applied to. If a pilot plan is successful, a Solution Implementation Plan is done to apply the chosen solutions to the organizations. Examples of tools are;
5S 5S (Sort, Set, Shine, Standardize, and Sustain) is a concept that focuses on achieving a better way to organize and manage the workspace. Kaizen (Continuous Improvement) Kaizen is a powerful approach that focuses on propelling a continuous turbine towards business improvement through continuous monitoring, analysing and implementing practices on improvements.
Poka-Yoke (Mistake Proofing) Poka-Yoke – in Japanese means “To avoid error” – focuses on the prevention of errors/mistakes before they occur. It involves detecting and erasing errors/mistakes during the manufacturing processes (Kumar, 2020). |
Training/Communication Plan | Training and Communication Plan is needed for the project team to communicate on what is going to happen withib the organization from the result of the project as well as identify what training can be used within the organization through the new system, machinery or process brought in from the project. |
CONTROL PHASE TOOLS/APPROACHES
This phase involves recording/documenting all improvements that are identified throughout the implementation of the project. The objective of this phase is to maintain the gains obtained from the Improve Phase, which is why standardizing the procedures is important to ensure that the new and improved processes are sustained. So, below are the tools/approaches used to help the objective of Control Phase;
Analysis of Before & After Improvements (Sigma Level) | An analysis of the improvements after the pilot testing in Improve Phase is needed to be done in order to see if there is any improvement in the process based on the Sigma level. and prove that the project goal is achieved Tools from the Analyse Phase can be used to analyse this part. |
Pilot Replication Plan | A pilot replication plan is carried out after the success of the pilot plan. This is done by replicating the changes or best solutions from the pilot plan throughout the organization rather than the small area initially used. |
Implementation/Handover Plan | An implementation/handover plan is given to the project owner by the project team handling the project so that the owner will be able to review the key elements of the project (schedule, work structure, resources, cost/budget, control and contingency plan) and implementing it throughout the organization. |
Control Plan | A ‘Control Plan’ is used to record the functional elements of quality control by determining, describing and monitoring process performance metric to ensure the quality standards and customer requirements are met. It also helps monitor the stability of the process performance and improvements, and ensure that the process data does not exceed the control limit. |
Statistical Process Control (SPC) | An SPC is a tool used to operate process efficiently using statistical method by applying the PDCA Cycle (Plan, Do, Check and Action) in order to meet product quality or productivity goals required by process. |
Individual and Moving Range (I-MR) Control Chart | The I-MR Chart is a tool that focuses on determining the stability or instability of a process. It is divided into two charts; ‘Individual Chart’ (monitors the process mean), and ‘Moving Range Chart’ (monitors the process variation for every time intervals). This tool deliver process variation evenly via graphical approach, and also helps analyse the time when a process is unstable as well as identify the cause. |
Dashboard Samples/SOPs/OPLs | The control phase also involves many documentation such as dashboard samples (a standard automated dashboard that help track key measures and benefits), Standard Operating Procedures (documented processes carried out within a company’s products and services), and One-Point Lessons (a tool for educating operators and improve product/service quality). |
Final Financial Benefits Calculations | Finalizing the Financial Benefits calculations is important in order to see the soft savings and hard savings earned from the project as well the improvements that are tangible and intangible |
WHERE CAN SIX SIGMA BE APPLICABLE?
The best thing about Six Sigma is that, with its methodologies and tools, it can be applied to almost any type of industry out there (Lean vs. six sigma, 2020) such as;
- Engineering industry
- Manufacturing industry
- Plant Operations
- Sales Marketing
- Customer Service
- Travel industry
- Healthcare
- Military
HOW DOES SIX SIGMA HELP IN PROJECT DELIVERY?
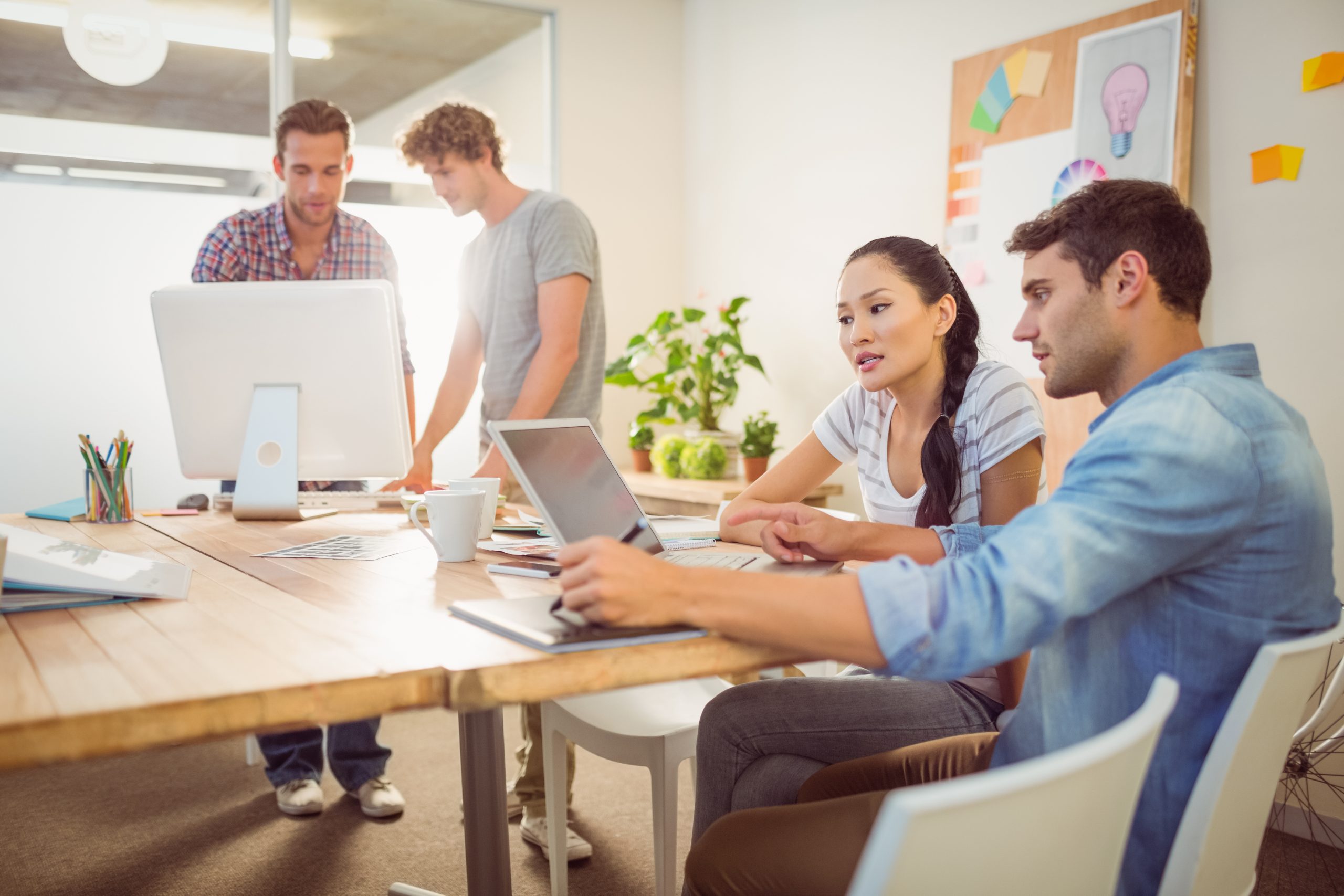
Six Sigma is a project-driven management approach that is widely used by many organizations to help improve their products, services, and processes – across various disciplines including production, product development, marketing, sales, finance, and administration – by continually reducing defects in the organization. It is a very effective business strategy that aims to improve customer requirement understanding, business systems, productivity, and financial performance.
According to Dhiraj and Deepak (2014), back in the mid-1980s, applications of the six sigma methods allowed many organizations to sustain their competitive advantage by integrating their knowledge of the process with statistics, engineering, and project management. Enabling Six Sigma in a project will greatly help an organization to achieve and deliver its goals and objectives through its management in financial results measurements, advanced data analysis tools and project management methodology application.
WHAT ARE THE ROLE STRUCTURES OF SIX SIGMA WITHIN SIX SIGMA ORGANIZATION?
In Six Sigma, there are officially a total of five level of certifications offered that can be obtained through the Six Sigma Accreditation Exams such as the International Association for Six Sigma Certification (IASSC) and the Council for Six Sigma Certification (CSSC). They are provided by many Six Sigma training and certification providers like MBizM Sdn. Bhd/Lean Sigma Experts Australia. Below shows the belt levels in Six Sigma standard from lowest to including their specifications.
Six Sigma Belt Levels | Specifications |
White Belt | – A beginner
– Have worked in teams on problem-solving projects – Posses basic Six Sigma knowledge |
Yellow Belt | – Have been a member of a project team.
– Have experience in reviewing project improvements. – Holds knowledge and comprehend the Six Sigma methodologies.
|
Green Belt | – Achieve a 3-year full-time employment (minimum)
– Obtain understanding on Six Sigma methodologies and tools for problem-solving – Obtain hands-on business transformation project experience – Received guidance for Black Belt projects regarding data collection and analysis – Have lead Green Belt projects |
Black Belt | – Achieved a 3-year full-time employment (minimum)
– Obtain work experience in a core knowledge field – Acquire proof of completion of two Six Sigma projects (minimum) – Demonstrate expertise in applying multivariate metrics to diverse business change setting – Lead diverse teams in problem-solving projects – Have trained and coach project teams
|
Master Black Belt | – Have attained Black Belt
– Achieved a 5-year full-time employment (minimum) – Acquire proof of completion of 10 Six Sigma projects (minimum) – Have a verified work portfolio with individual specific requirements – Experienced in coaching and training Green and Black Belts – Developed key metrics and strategies – Worked in an organization as a Six Sigma technologist and internal business transformation advisor |
WHAT ARE THE BENEFITS OF BEING SIX SIGMA CERTIFIED?
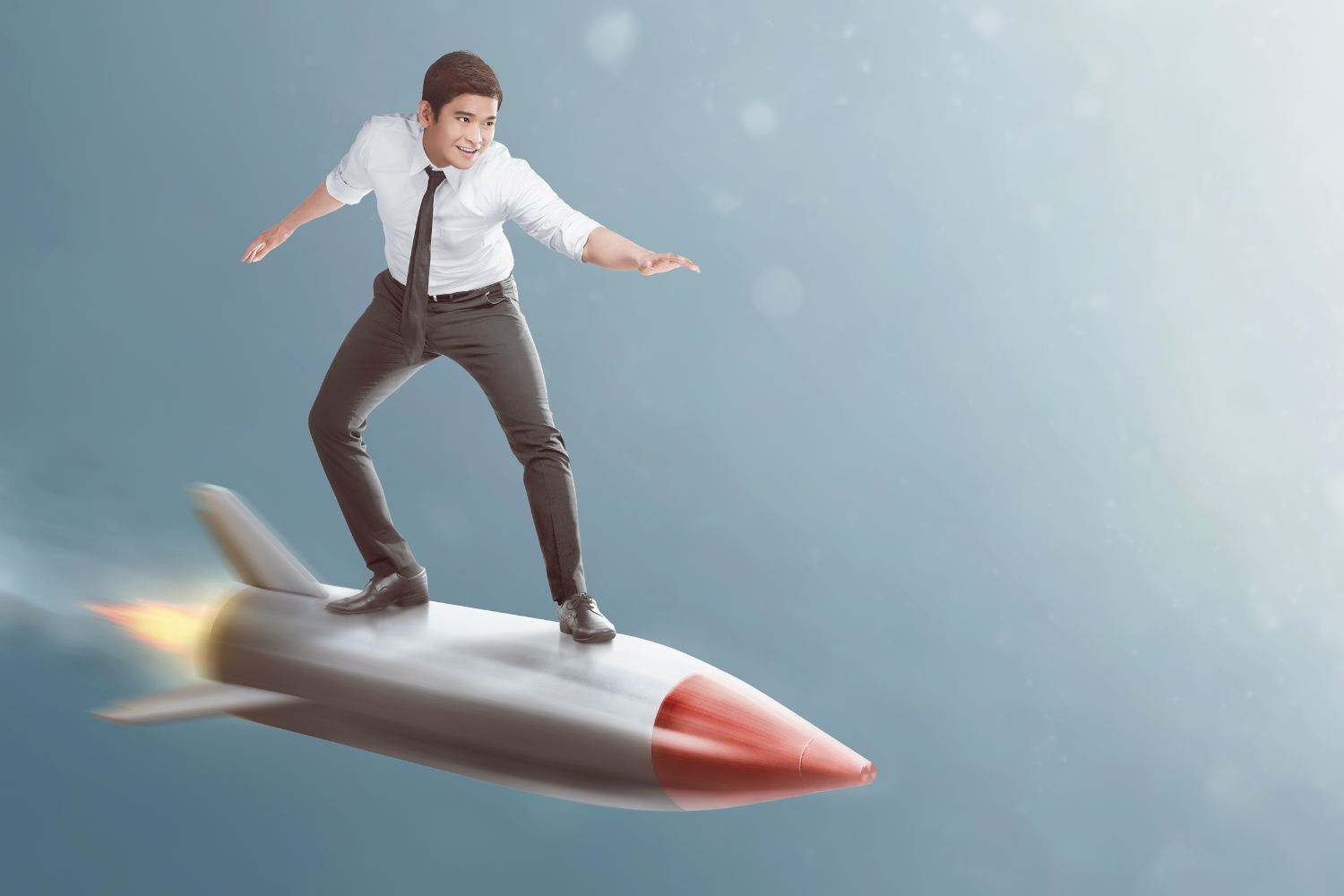
Learning and applying Six Sigma, let alone achieving its Belt certification, can benefit a person and an organization tremendously (Kumar, 2020; Mehrotra, 2017). For example;
Career Opportunities
- Business Process Manager
- Team Leader
- Supervisor
- Manager
- Senior/General Manager
- Programme/Project Manager
- Analyst/Business Analyst
- Continuous Improvement Manager
- Quality Assurance Manager
- Consultant
Personal Gain
- Career Advancement
- Nurture Managerial and Leadership Ability
- Standardization
- Improve Business Processes and Sustain Quality Improvement
- Excellent Salary
- Applicability Across Industries
- Ensure Compliance
- Gain Hands-on Experience in Quality Management
- Better Understanding
- Organizational Growth
- Support Your Organization Eliminate Errors
Organizational Benefits
- Customer Satisfaction
- Improved Bottom Line
- Employee Satisfaction
- Better Partnerships
JOIN US!
If you are ever interested to learn more and join our Six Sigma or Lean Six Sigma courses, we encourage you to visit us at https://www.mbizm.com/ or leansigmaexperts.com.au/, register you details and we will help you get started on your Six Sigma journey!
In our courses, we provide three types of trainings; Public Training, In-House Training and Online Training where you will be given learning materials on the fundamentals of Six Sigma/ Lean Six Sigma, as well as have experienced Black Belt consultants to teach you more about them.
How about it? Go and register now and we will see soon!
Bibliography
Aruleswaran, A. (2009). Changing with lean six sigma. Petaling Jaya: LSS Academy Sdn. Bhd.
Bhoraniya, N. (2019, December 2). DMAIC methodology in six sigma l Complete overview. Retrieved from Nikunjbhoraniya.com: https://www.nikunjbhoraniya.com/2019/12/dmaic-methodology-in-six-sigma.html
Dhiraj, K.,& Deepak, K. (2014). A review of six sigma approach: Methodology, obstacles and benefits. Global Journal of Engineering, Design & Technology, 3(4), 1-5.
DMAIC – The 5 Phases of Lean Six Sigma. (2020, January 31). Retrieved from https://goleansixsigma.com/dmaic-five-basic-phases-of-lean-six-sigma/
History of six sigma. (2018). Retrieved from Quality gurus: https://www.qualitygurus.com/history-of-six-sigma/
Kumar, P. (2020, February 28). What is six sigma: A complete overview. Retrieved from SimpliLearn: https://www.simplilearn.com/what-is-six-sigma-a-complete-overview-article
Lean vs. six sigma. (2020). Retrieved from Planview Leankit: https://leankit.com/learn/lean-vs-six-sigma/
Mehrotra, S. (2017, December 19). Six sigma certification: What does it benefit your career & organization? Retrieved from Greycampus: https://www.greycampus.com/blog/quality-management/six-sigma-certification-how-does-it-benefit-your-career-and-organization
Olofsson, O. (n.d.). History of quality management. Retrieved from World class manufacturing: https://world-class-manufacturing.com/Sigma/history.html
Pepper, M. P., & Spedding, T. A. (2010). The evolution of lean Six Sigma. The International Journal of Quality & Reliability Management, 27(2), 138.
Salah, S., & Rahim, A. (2019). The integration of Six Sigma and Lean. In An Integrated Company-Wide Management System (pp.49-93). Springer, Cham.
Six sigma DMAIC process – Define phase – Capturing voice of customer (VOC). (2020). Retrieved from Six sigma institute: https://www.sixsigma-institute.org/Six_Sigma_DMAIC_Process_Define_Phase_Capturing_Voice_Of_Customer_VOC.php
Six sigma fundamentals: DMAIC vs DMADV. (2014, June 17). Retrieved from Six sigma daily: https://www.sixsigmadaily.com/six-sigma-basics-dmaic-vs-dmadv/
What are the differences between six sigma, lean and lean six sigma. (2020, January 7). Retrieved from Villanova university : https://www.villanovau.com/resources/six-sigma/differences-between-six-sigma-lean-and-lean-six-sigma/
What is DMADV? (2012, December 10). Retrieved from SIx sigma daily: https://www.sixsigmadaily.com/what-is-dmadv/
What is process mapping. (2020). Retrieved from Lucidchart: https://www.lucidchart.com/pages/process-mapping