Wastes In Lean Six Sigma
Optimizing processes to eliminate Wastes In Lean Six Sigma is crucial to ensure your company’s success. There are consequences if you continuously produce waste in the process, such as lower profitability, increased customer costs, decreased product quality, and employee satisfaction. Therefore, as a business owner, you need to identify the non-value-adding activities and improve the process to avoid wasteful activities.
Lean or Lean Six Sigma is known in the manufacturing industry, and over the past few years, it has been widely introduced and used by other industries as well. Lean manufacturing is a management philosophy derived from Toyota Production System, which focuses on eliminating waste. It considers many kinds of waste, including the waste of excessive human movements. It integrates each step of production into a holistic, efficient process that reduces cost and improves the overall revenue. Therefore, under lean manufacturing, seven Wastes In Lean Six Sigma are identified: transport, inventory, motion, waiting, over-processing, overproduction, and defects. In the manufacturing system, this is called “Muda.”
What is waste? The easiest way to describe waste is that it adds no value to the process or its product. As a customer, you may not be happy to be in that situation as you are paying for any action that does not add value to what you want. Imagine paying for the foods you did not order in the restaurant with the meal prepared not according to the restaurant’s standard. Would you argue and demand the extra charges be removed from your bill? Would you want to pay for the machine operator’s wages when they sat unproductively and just waiting for a delivery or for the rework processes undertaken due to the incorrectly set machine? These are all wastes included within the cost of the products or services you give. It is either inflating the price you pay or reducing the company’s profit.
The acronym for the seven deadly wastes in Lean is known as T-I-M-W-O-O-D. Transportation, inventory, motion, waiting, overproduction, over-processing, and defects.
Transportation

Transportation waste is a waste when you move resources which is the material, and the movement does not add value to the product. Hence, excessive movement of materials can be costly to your budget and may cause damage to the quality. Apart from that, excessive movement of people and equipment may cause unnecessary work, exhaustion, and greater wear and tear. Excessive movement does not apply only to products. It also happens in the work office setting, where workers who collaborate should be seated closer. This is because it is easier for them to discuss the projects they are working on together. Meanwhile, in the factory setting, materials used for production should be easily accessible at the production location, and workers should avoid double or triple handling of materials.
Inventory

Excessive inventory results from a company holding ‘just in case’ inventories. In such cases, companies overstock themselves to meet unexpected demand and avoid production delays, low quality, and other problems related to the piles of inventory. Office inventory waste could be unused files waiting to be worked on, customers waiting for their enquiries to be answered, papers from unused materials for the clients, or any obsolete files are considered as in-office inventory waste. Meanwhile, manufacturing inventory waste includes broken machines sitting around inside the factory compound. More finished products than the demand or finished end products cannot be sold. Countermeasures that can be taken to curb inventory waste include purchasing raw materials only be made when needed to reduce buffers. However, always remember that excessive inventories have nothing to do with customer satisfaction and do not add value. Inventory Wastes In Lean Six Sigma only increases storage and cost depreciation.
Motion

Motion waste means movements made by the employees or any machines which are complicated and unnecessary. These unnecessary movements may cause extended production time or, even worse, it may cause injuries in the factory during the production is ongoing. In other words, do whatever is necessary to arrange a process where workers need as little as possible to finish their job.
Motion waste includes unnecessary movement of equipment, people, or machinery. This includes lifting, reaching, bending, walking, stretching, and moving. In the office setting, motion waste can be varied. It includes walking, searching for physical files, reaching to get materials, looking through the inventory to look for what is needed, excessive mouse clicking, and double data entry. Meanwhile, motion waste in manufacturing is walking to get a tool or materials, readjusting a component after it has been installed. Tasks that require excessive motion should be redesigned to enhance personnel’s work to increase the health and safety levels. Some countermeasures that you can take to curb motion waste are making sure the employee’s workspace is well organized, placing equipment near the production location, and putting materials in an ergonomic position to reduce stretching and straining.
Waiting
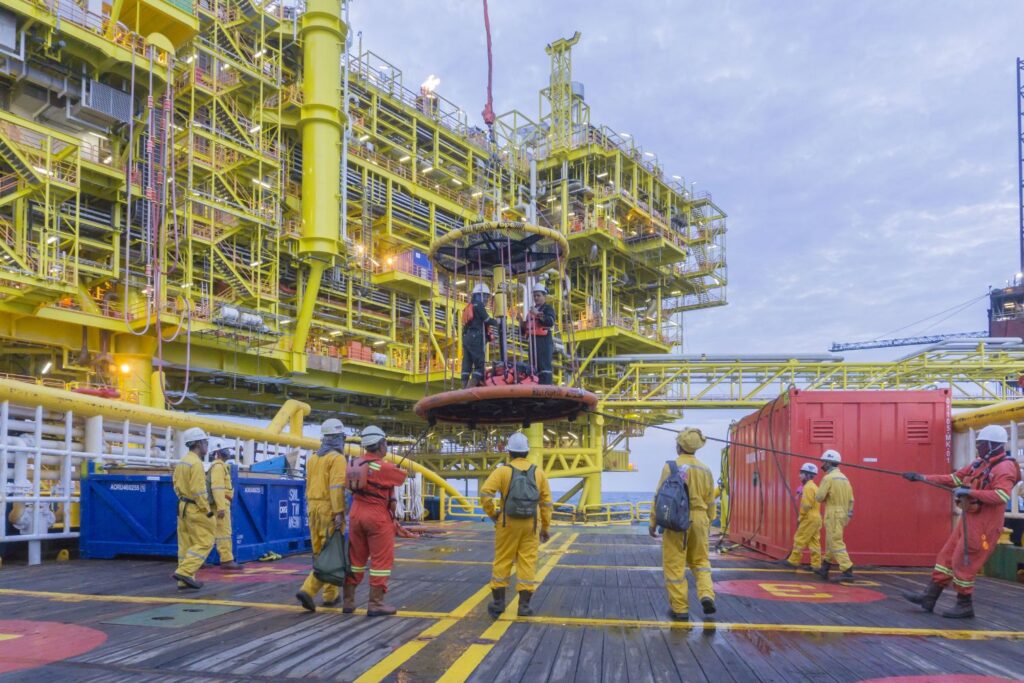
One of the easiest wastes that people recognize and always do is the waiting waste. It is easily identifiable to be delivered, equipment waiting to be fixed, or a document waiting for executives’ approval. Whenever goods or tasks are not moving, the waiting waste occurs.
The waiting waste can be classified as waiting for people or equipment, which often causes unevenness in the production stations and may result in excess inventory and overproduction. In the office environment, waiting waste includes waiting for your colleagues to respond to an email, piles of files waiting for review, ineffective meetings, and waiting for the computer to load a new tab or programme. Meanwhile, in the manufacturing industry, waiting waste shall include waiting for the materials to arrive, workers waiting for the instruction to start manufacturing, and having equipment with insufficient capacity.
You can take countermeasures to avoid waiting waste by designing a process to ensure continuous flow, segregating the workload using standardized work instructions, and developing skilled workers who can juggle and quickly adjust to the work demands.
Overproduction
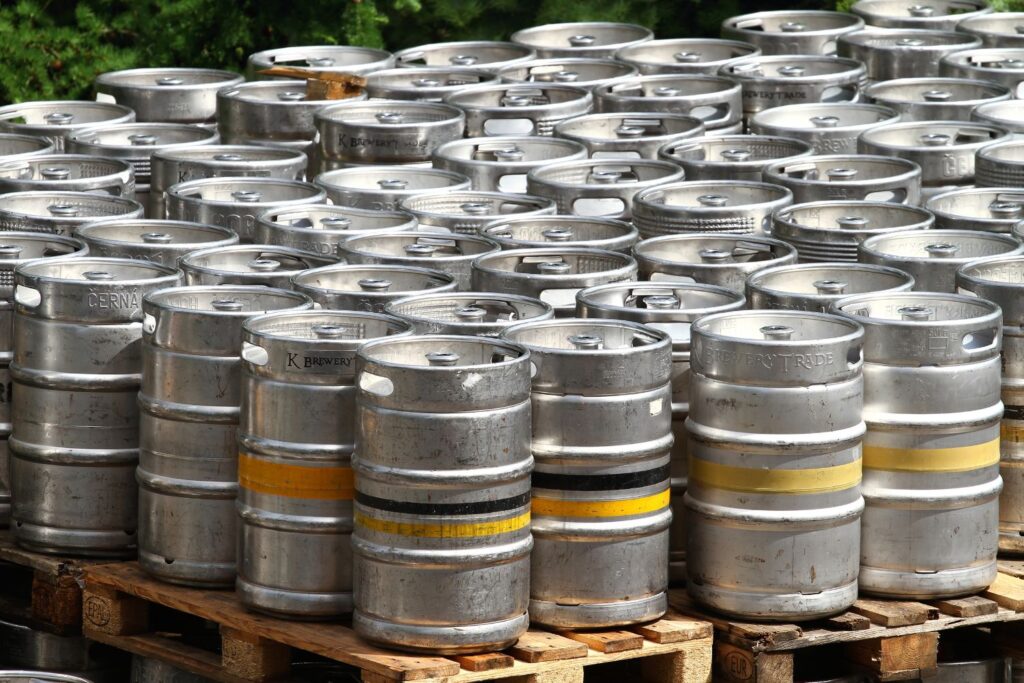
Keep in mind that waste that the customer is unwillingly paying for. Overprocessing means you have exceeded the customer’s demand, which will only lead to additional costs. It adds up to the current cost because it requires additional transportation, excessive motion, and a longer waiting time. Not only that, if there are defects appear during the overproduction, your team will need to rework more units.
Overproduction occurs when you are producing a product before it is required. Understandably, it might be tempting to produce as many products as possible. Rather than making extra products just when needed under the Just in Time philosophy. The just in case way of working leads to many problems, including preventing the smooth flow of work, higher storage costs, hiding defects inside the WIP, requiring more capital expenditure to fund the production process, and excessive lead time.
Additionally, over-producing a product also increases the likelihood that the product or quantities produced are beyond the customer’s requirements. In an office environment, overproduction could include printing errors or making extra copies, creating reports that no one reads, using new blank papers for something unimportant, and providing a service before the customer is ready. The countermeasure for overproduction is using a Takt Time to ensure the manufacturing rate between stations is even. You can use a Kanban system to control the amount of work in progress (WIP).
Overprocessing
- Using higher precision equipment that is necessary.
- Using components with capacity beyond what is required.
- Running more analysis than needed.
- Adding up more functionalities in a product than needed.
This kind of Wastes In Lean Six Sigma reflects on works that don’t bring additional value, or the job is getting more deals than required. These extra works can add other features to the products that nobody will use, but they increase your business costs. For example, if a car manufacturer installs a TV screen in the back seat, it may only be used if you have a small kid inside the car. Not everyone will find it enjoyable to watch a TV while the car is moving, especially if you have motion sickness. This kind of waste reflects on works that don’t bring additional value, or the work is getting more value than required. In the manufacturing industry, overprocessing could include:
Meanwhile, overprocessing can include generating more detailed reports than required, unnecessary signatures on a document, or extra workflow in the office setting.
One simple way to avoid overprocessing is to better understand the work requirements from the customer’s standpoint. Always think about your customer before starting work. This will help you produce a product or service to the quality and expectation that the customer desires and produce only the quantities needed.
Defects
Defects happen when the product is not fit to be used, which typically results in either reworking or scrapping the product. Either way, both results are wasteful as they add additional costs to the operation without giving any value to the customer. There can be a few countermeasures to avoid defects:
- Look for the most frequent defect and focus on it.
- What you can do is design a process to detect if there are any abnormalities and make sure it does not pass any defective items along the production process.
- You can redesign the process so that it does not lead to making any defects.
- You can use standardized work to ensure a consistent manufacturing process that is defect-free.
As a business owner it is crucial for you to identify the seven deadly Wastes In Lean Six Sigma in the producing process of your products or services. This to ensure the products or services that your company produced is following the requirements or standard operation procedures that could satisfied your customers.
Lean Sigma Experts Australia provides various Lean Six Sigma training stages such as Yellow Belt, Green Belt, Black Belt, and Master Black Belt. Our consultants and trainers are Lean Six Sigma certified, and they have conducted training for many years for clients in different industries. For your information, Lean Sigma Experts Australia is an Accredited Training Organization, Curriculum Provider and Examination Center by IASCC and by Council for Six Sigma Certification. We offer the best price for Lean Six Sigma Training in Australia with certified trainers and complimentary training materials. If you wish to learn more about process mapping and Lean Six Sigma training, visit our website at https://leansigmaexperts.com.au to learn more about our Lean Six Sigma programmes.